This is how the Backforce One is made - Marco visits Interstuhl's production!
A report like this is available for the first time today. It is the first time that I was allowed to see the production of a gaming chair myself and also film it. So I am proud to present you some exclusive impressions of the production of the Backforce One.
As you could already read in my ▷ Backforce One review, the gaming chair is produced by Interstuhl in Germany – Meßstetten Tieringen.
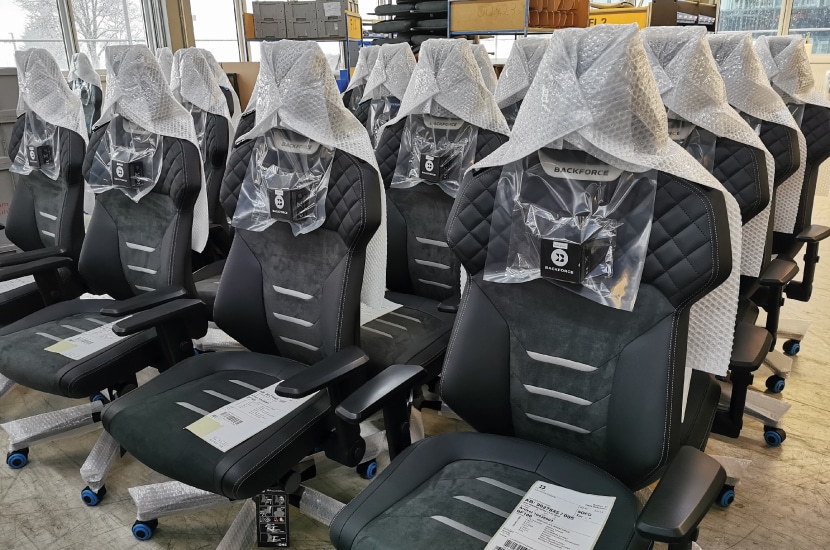
Interstuhl itself has around 650 employees and is still an owner-managed family business. The company has been around for more than 50 years, which means that more than 50 years of experience have gone into the design and implementation of the Backforce One. Insights into the production of this chair Made in Germany you get now via video & in this report. Have fun!
Of course, I can’t show you every single production step up to the finished product. But there are some very interesting insights in any case.
The sewing - backrest quilting pattern
We’ll start with the shoulder area of the backrest. More specifically, we’ll look at how the backrest gets its very handsome design.
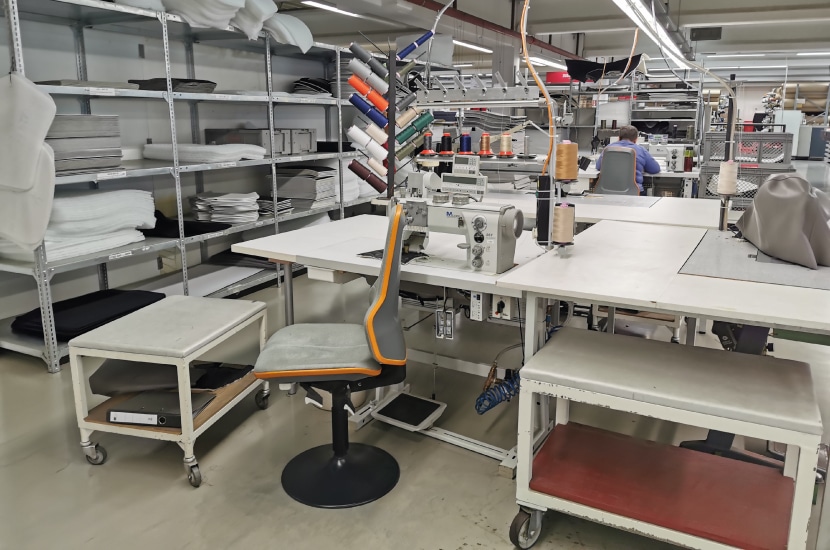
This is the workplace of a seamstress at Interstuhl.
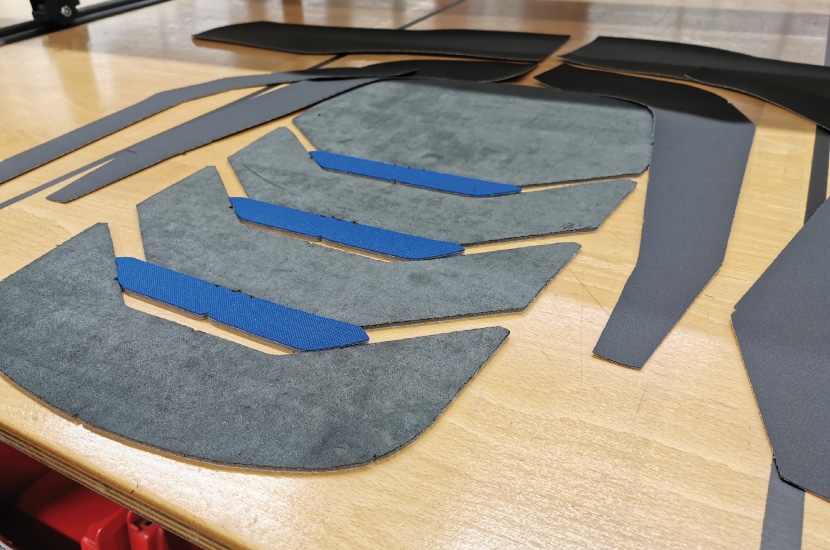
Here we see cut patterns for the individual cover components of the BF One.
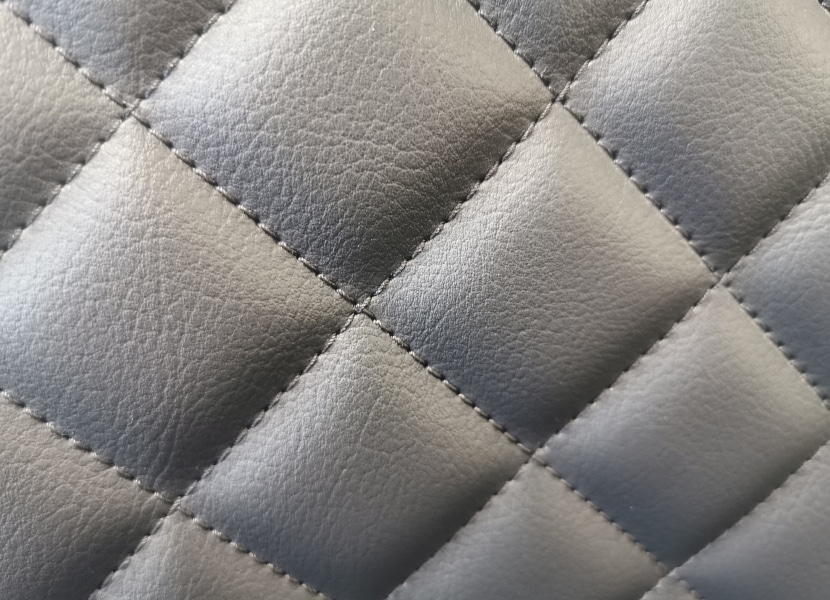
To create this beautiful quilting pattern, work as follows:
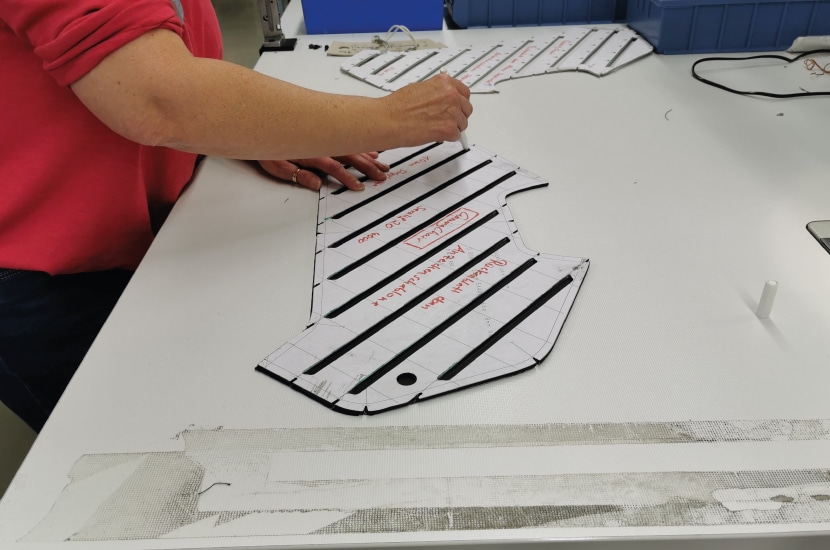
But first of all, a template is applied and a pattern is drawn. On each of these drawn lines is sewn the same to create the pattern.
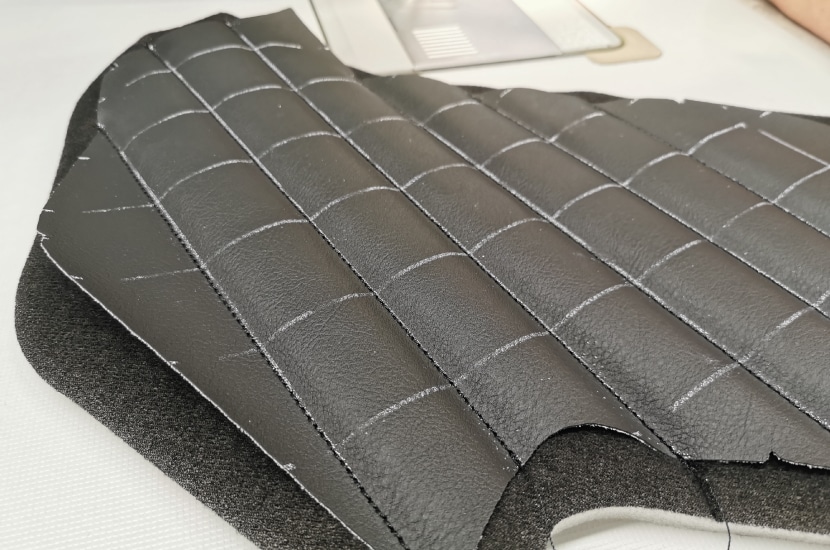
Under the imitation leather is a foam. It is there so that the quilting pattern is nicely visible at the end. The fact that there is foam under the sewn-on leather creates the padded curves.
Foam plant - How seat foam & back foam are produced
In this section we look at how the upholstery foams for the seat & backrest are produced.
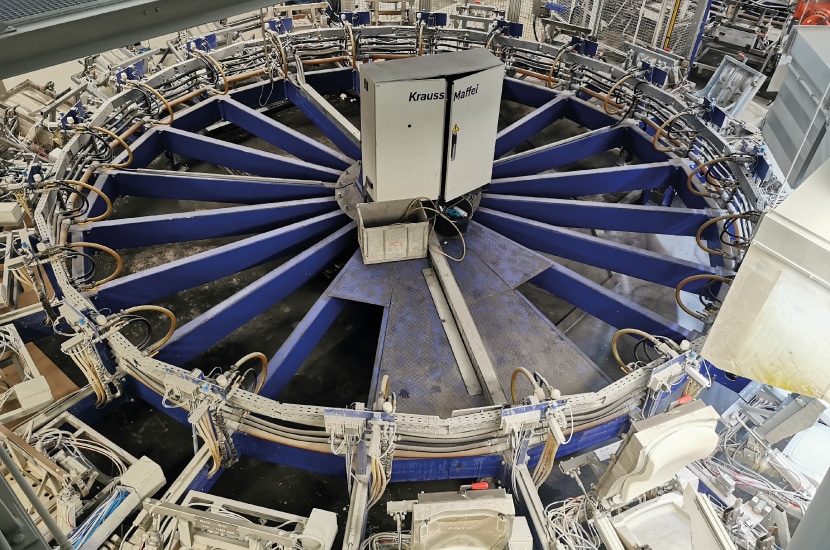
This is a foam system from above. The base compound for the upholstery foam is poured into the molds, which resemble a waffle iron purely in terms of function.

A robot arm independently fills the molds with the base material for upholstery foams.
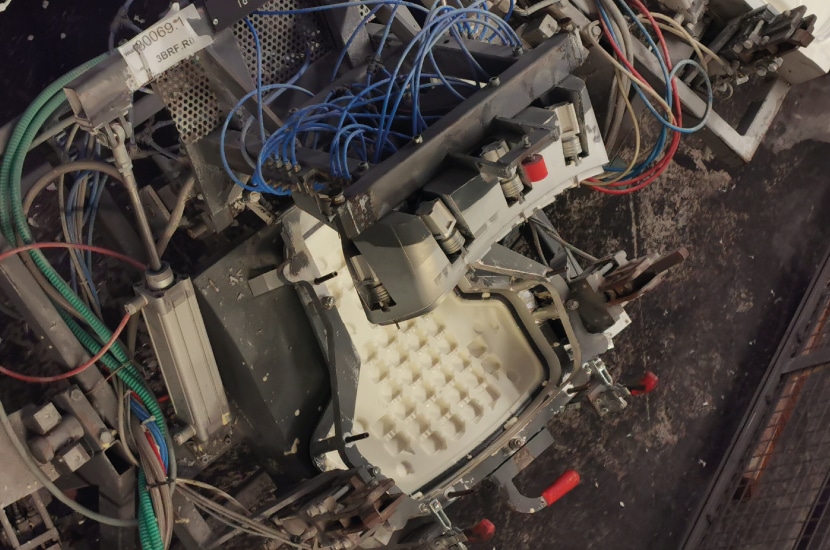
It takes 8 minutes and needs 60°C until the upholstery foam is ready.
Sustainability: Normally, these molds are wetted with silicone so that the finished foam can be easily released. At some point, however, the company asked itself whether wax could also be used to make production a bit more sustainable. It was recognized that wax works without any problems, so the molds are wetted with wax here.
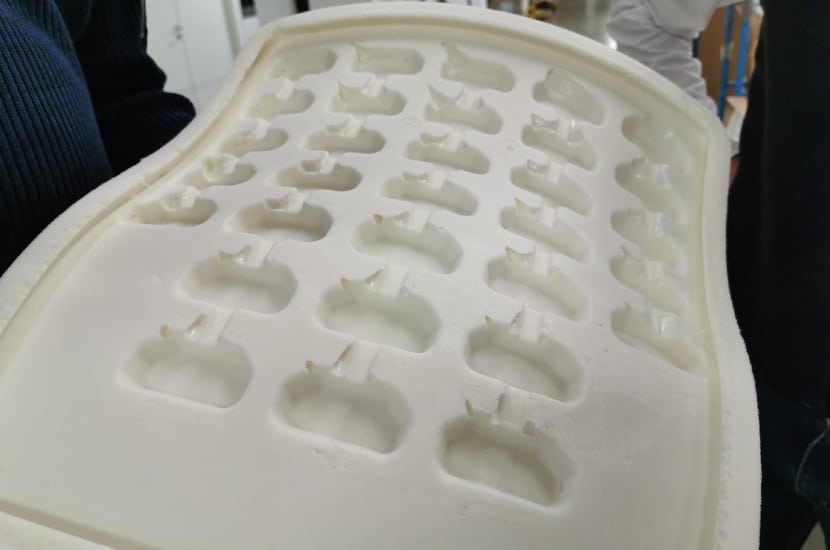
There are air holes in the foam of the seat. These ensure that the air escapes when you lean against it. This helps make the upholstery as breathable as possible.
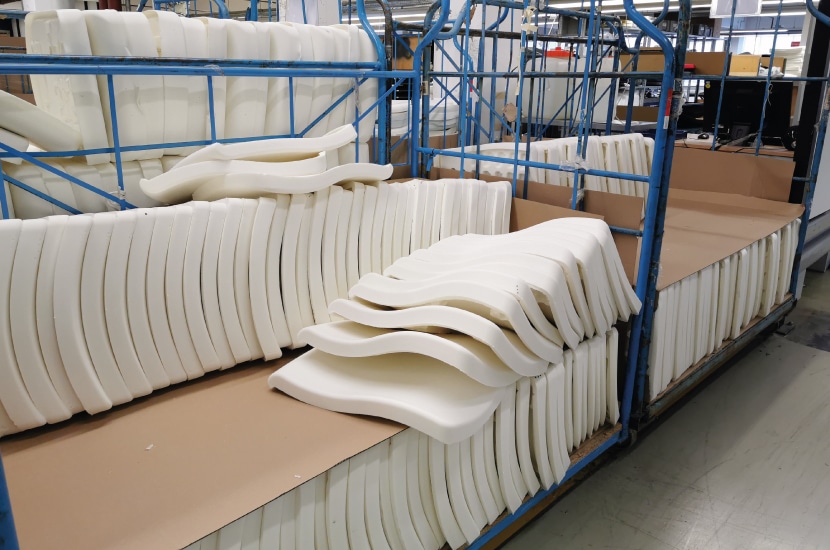
The foams are stored here for a short time until they are directly processed further.
Production of the back foam
Now let’s look at how the upholstery foam for the backrest is produced.
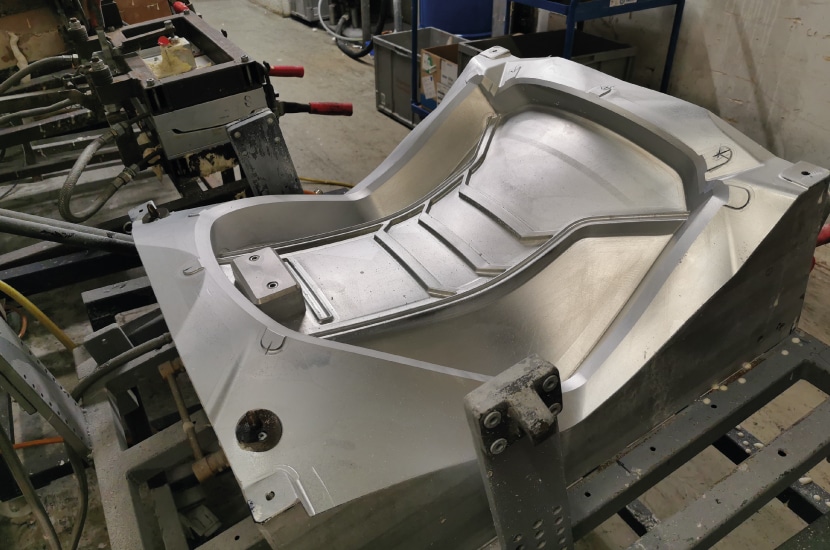
This is the tool, i.e. the mold for the production of the back cushion, into which the liquid base mass is immediately poured.
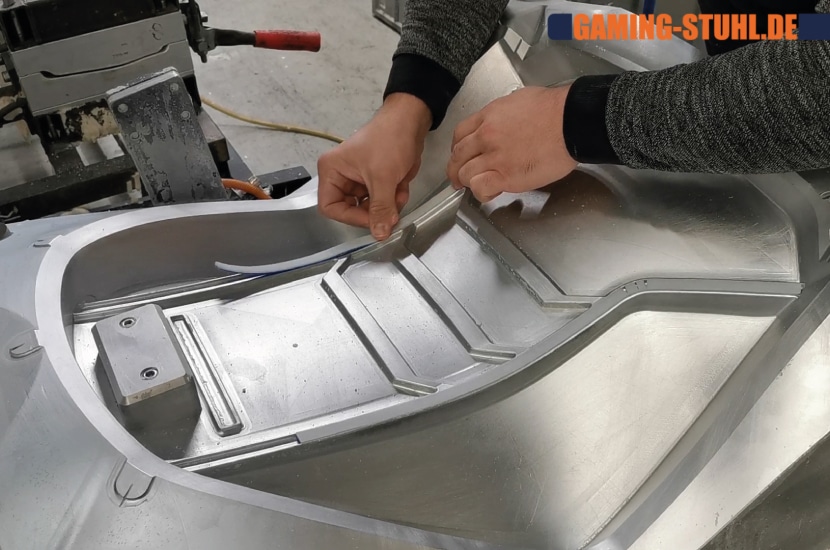
Before that, however, Velcro must first be inserted at the points provided for this purpose. The cover will be fixed to the Velcro tape later, as we will see. The Velcro will bond with the foam when it is foamed.
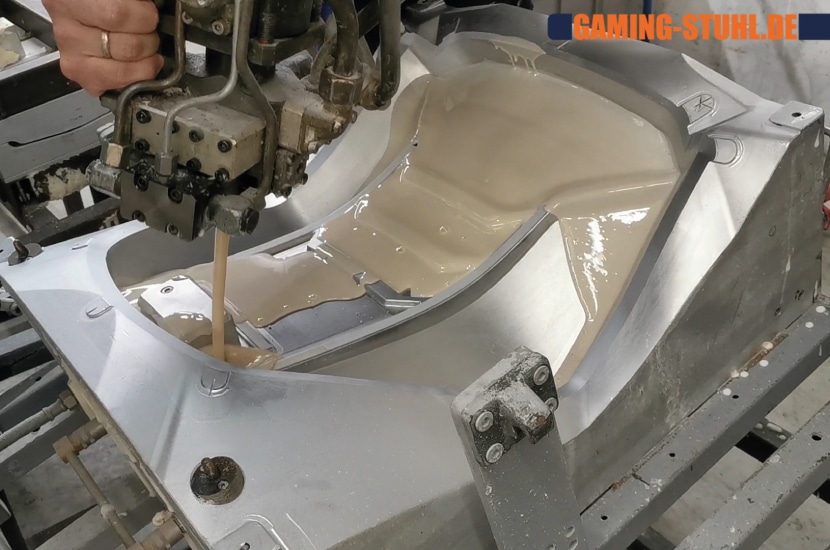
Now the liquid mass is filled into the mold and distributed. The process is comparable to a waffle iron. Little base material comes in, which then rises, so to speak, through the mold heated by means of hot water within 8 minutes.
8 minutes later we can see the product:
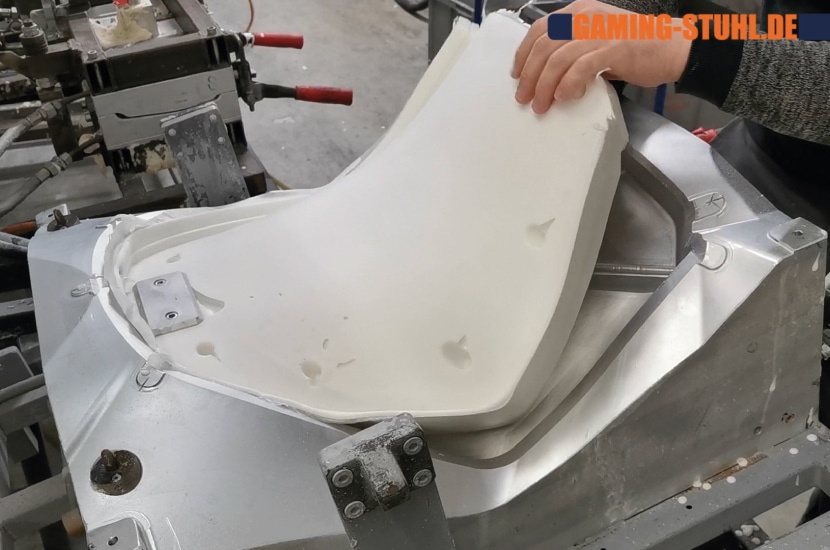
The excess around the edge is still cut off, of course, to get a completely clean shape.
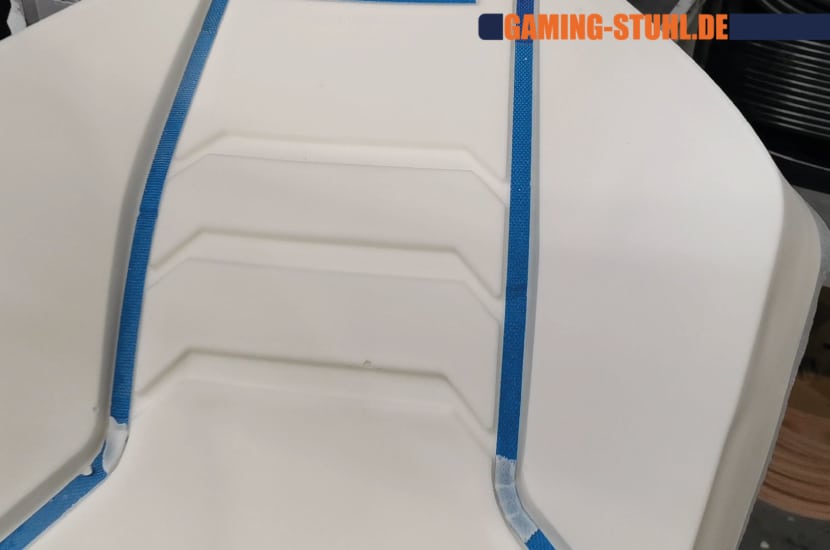
You can also see very nicely how the padding & Velcro have bonded together.
Processing of the backrest in upholstery
Now let’s take a look at how Richard refers to the backrest. Richard did his training at Interstuhl and has been employed there ever since.
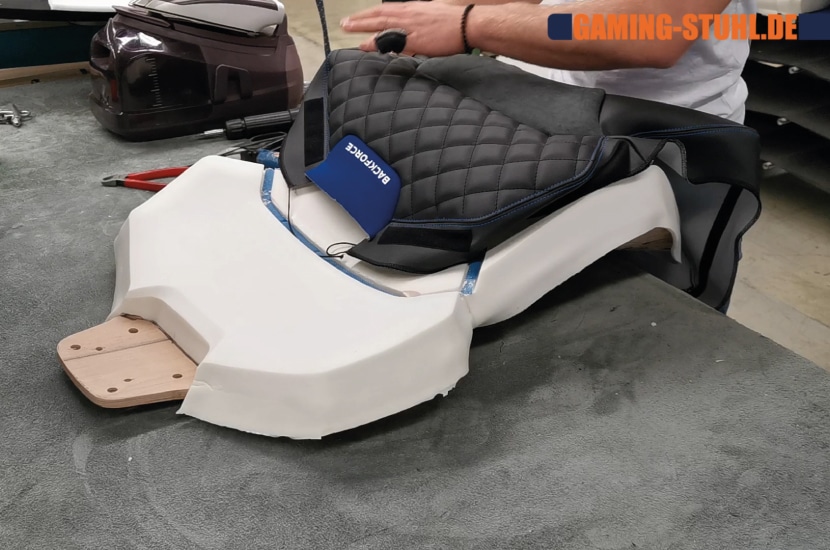
The foam part has already been provided with the back wood.
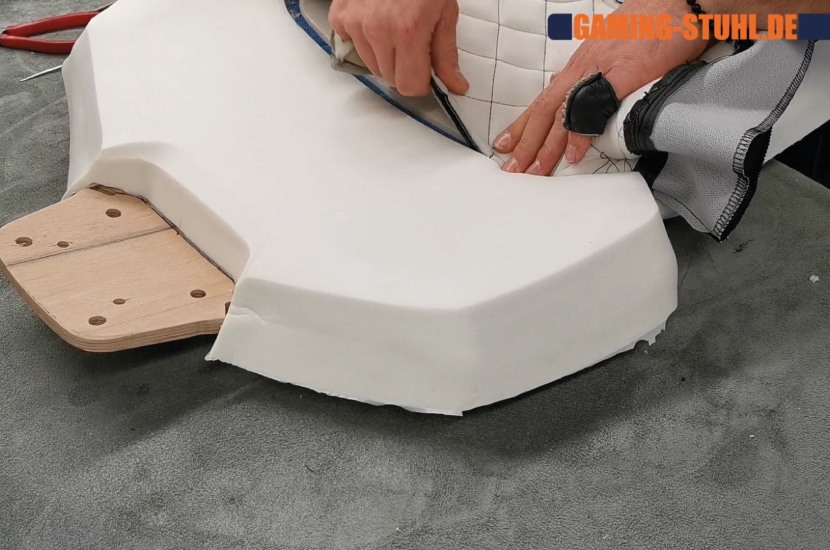
Here he fixes the cover to the hook tape. Actually, you usually say Velcro tape, but for Velcro you need two tapes: One time the loop tape and then the hook tape, which fixes the loop tape.
The blue tapes are hook tapes. The seam is fixed. Without the hook tape, the material would expand and slip in the long run. The cover would hang over the backrest like a sack.
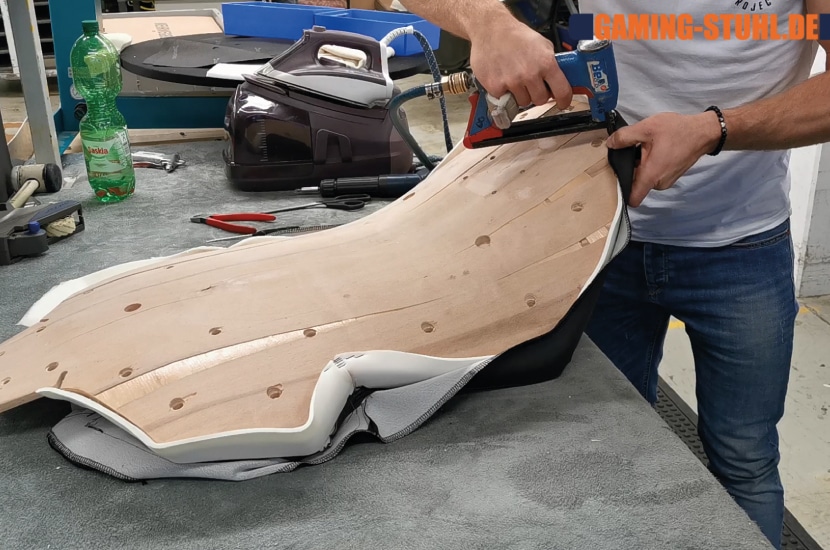
During the process, we constantly check whether everything is sitting as it should. Everything has to sit evenly, there is no wild tacking around. The process is much more difficult than it looks.
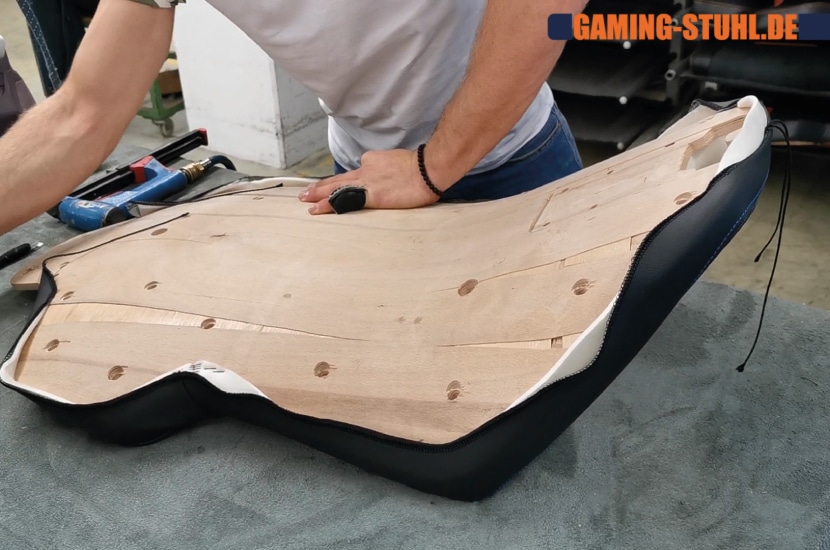
By the way, this protection on the fingers is so that the materials do not cut into the fingers. A glove would be too obstructive, the sensitivity would be lost. That is why there is such a fingertip protection.
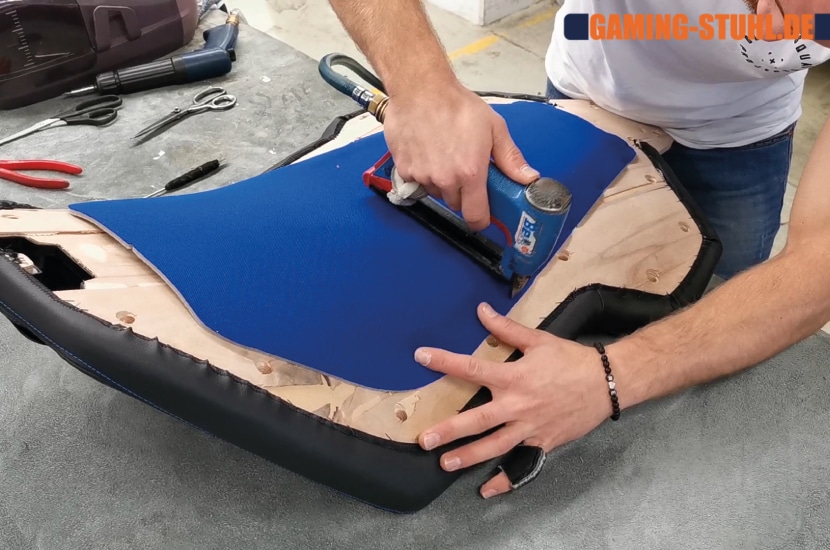
Now on the back of the backrest is still a thin foam, on which, in turn, is attached, in this case, a blue mat.
Depending on the chosen chair color, of course, the color of this component also differs – in the case of an orange chair, it is correspondingly orange. The plastic trim to be mounted later has cutouts, so you can see this color in the final product.
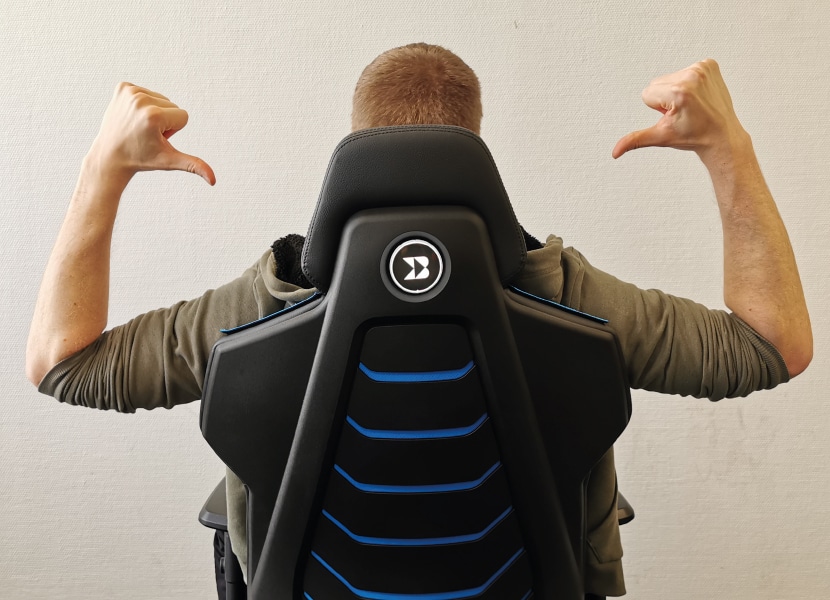
In my eyes, this is an important and interesting step. This process in particular makes the Backforce One an eye-catcher from behind as well. When we sit on the chair, we don’t notice much of the design.
However, as soon as we are no longer at the computer and push the chair to the table, it makes a really good picture from behind. Where most gaming chairs are plain black from behind, the Backforce One looks good exactly where you see it most often.
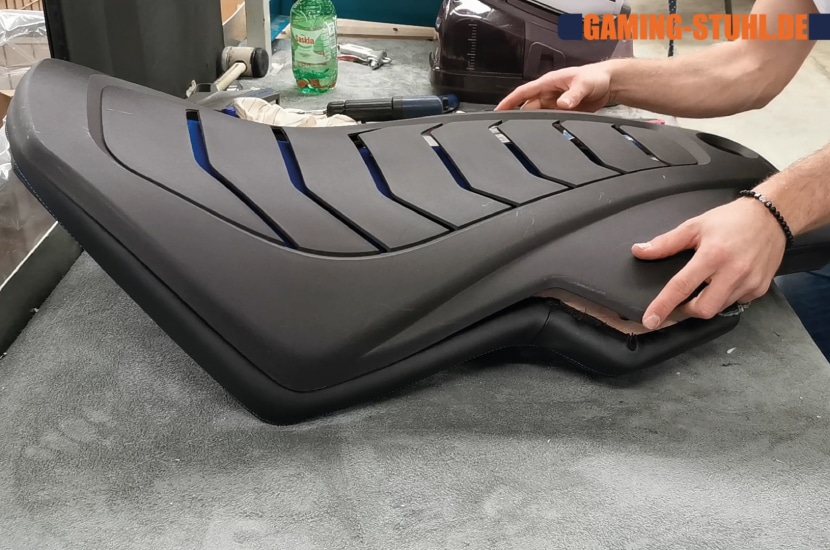
The plastic covering of the backrest is only stopped here to see if everything is correct. This is only a sample, the actual assembly takes place in another area.
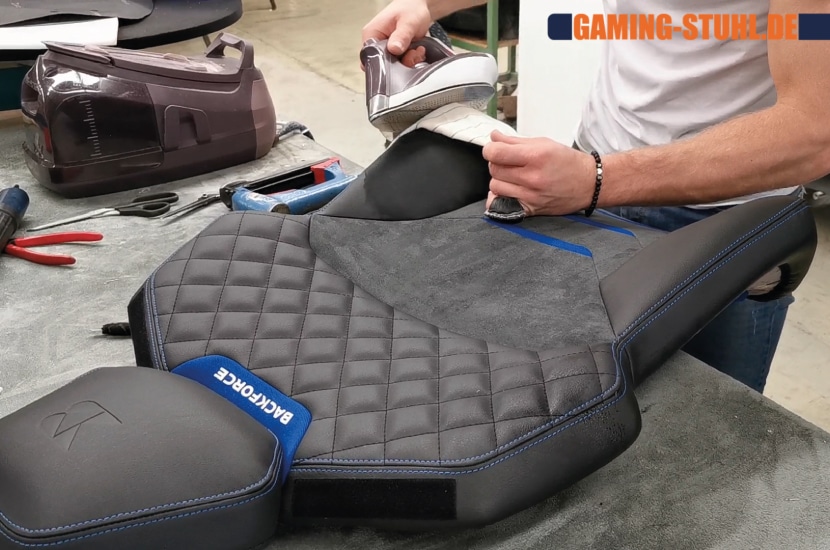
Finally, the material is steamed again. Steaming causes the material to contract additionally. Now the backrest is ready for the next step!
Welding - an indestructible back bracket
Next, we stopped by the welding shop. There were no welding processes to look at, but we did take a look at the Backforce One’s backrest bracket, which connects the backrest and seat mechanism at the backrest.
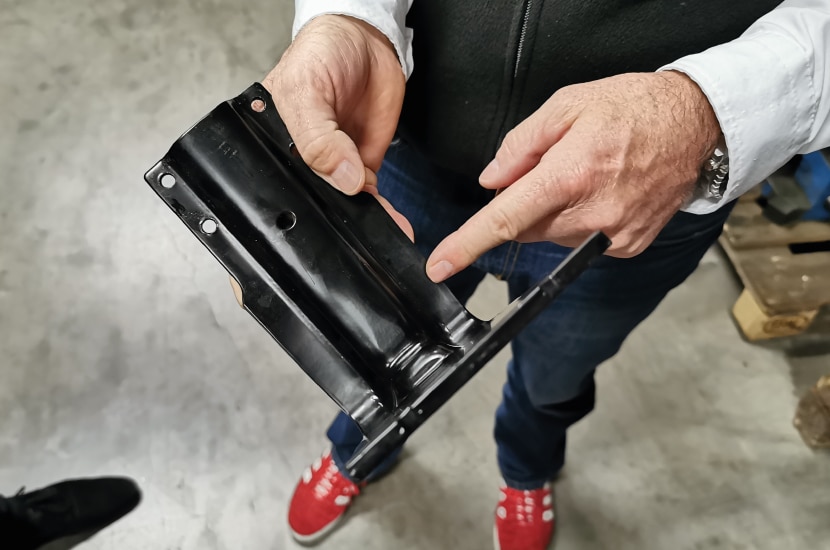
This part is only stamped in the welding shop. The shaping is exactly as intended, it provides a much higher stability, which in combination with the steel thickness and the design is made for eternity.
You can bend and break the part as you like, it does not move a millimeter.
Final assembly - the last steps
We have now arrived at final assembly, where the final steps in the production of the Backforce are being taken.
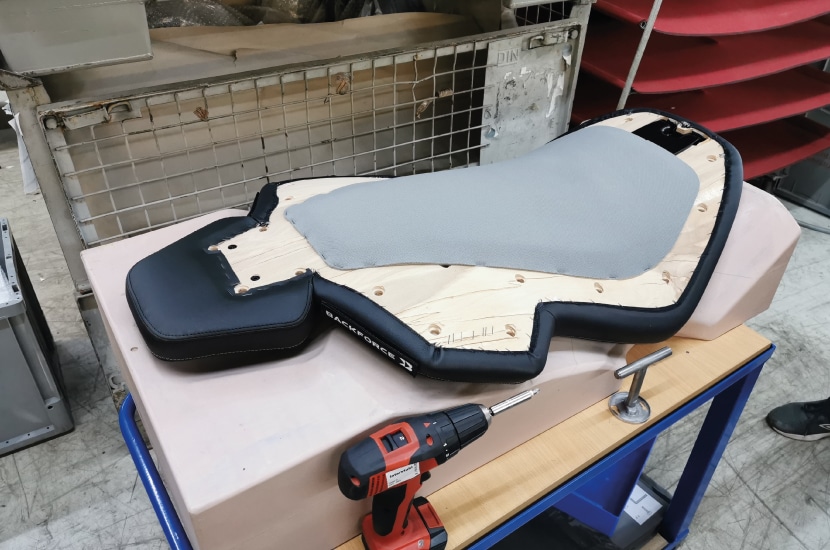
Here we see the backrest, on which the plastic trim is about to be applied.
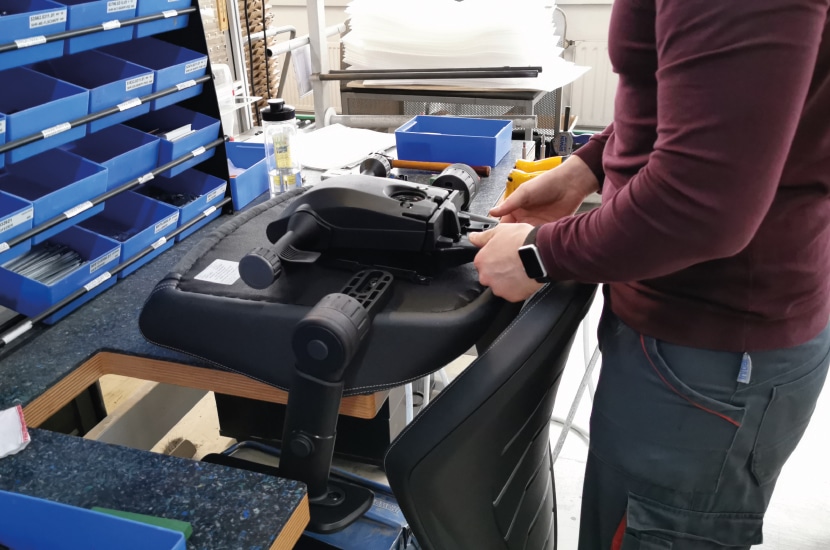
In this step, the mechanics are assembled to the chair. This process is called marriage – just as car builders do when the transmission & body are joined. So with car builders, as with chair builders, the joining of the heart of the product is called “marriage”.
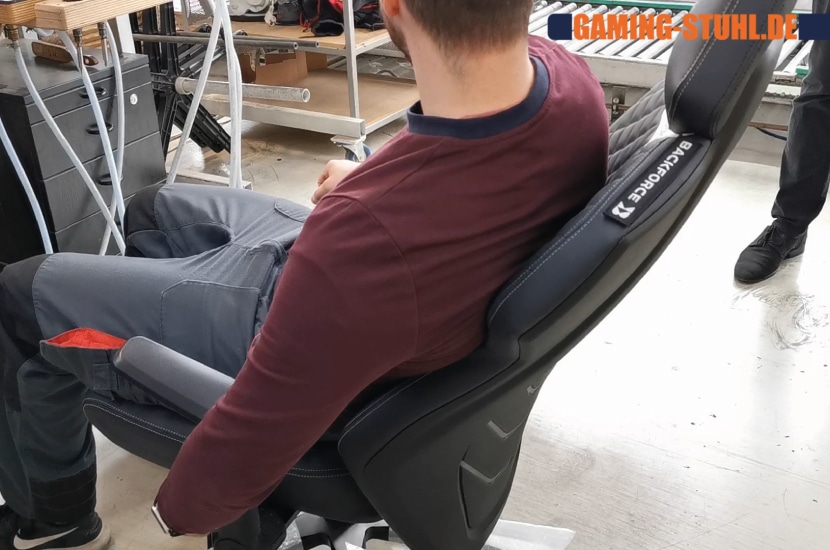
At the end, the employee checks the chair again for its functions, i.e. checks whether everything is working properly.
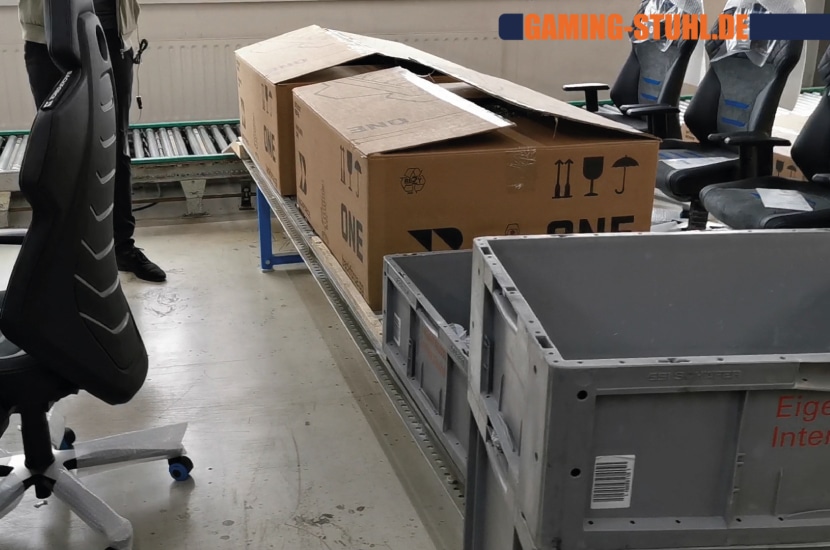
I also find the packaging here nice by the way. This can be used for the assembly of the chair. You put the backrest according to the silhouette and can thus easily assemble the seat mechanism without having to balance the screw holes.
This can be really annoying sometimes. The idea for this came from one of the very dedicated employees, the idea was successfully implemented and is now a pleasant assembly aid for every Backforce One buyer.
Shipping and quality control
I personally found this department very interesting as well. The Backforce One is not processed here, but only some of the many other chairs from Interstuhl – but still a very exciting thing.
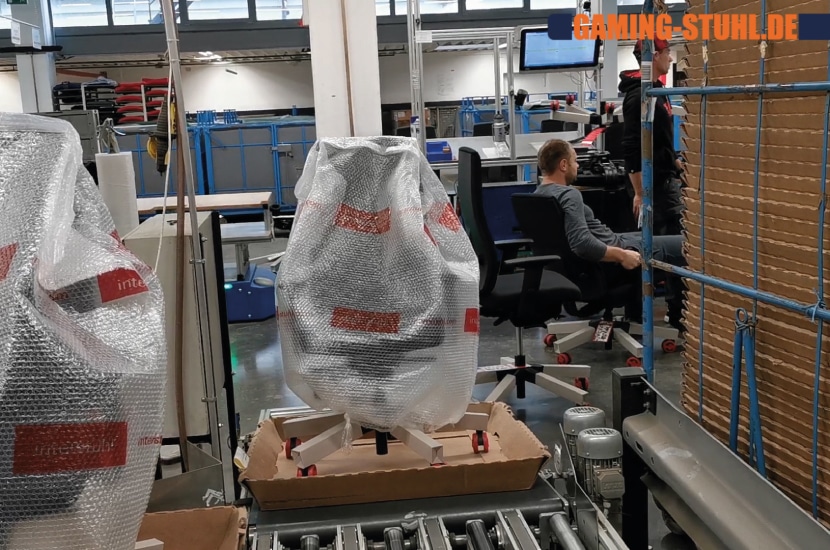
Here, too, an employee checks the function of each chair.
The chair is then placed in a cardboard shipping ship and onto a conveyor belt. And this is where it gets interesting: The chair now has to go to the shipping department, which is located in the next but one part of the building.
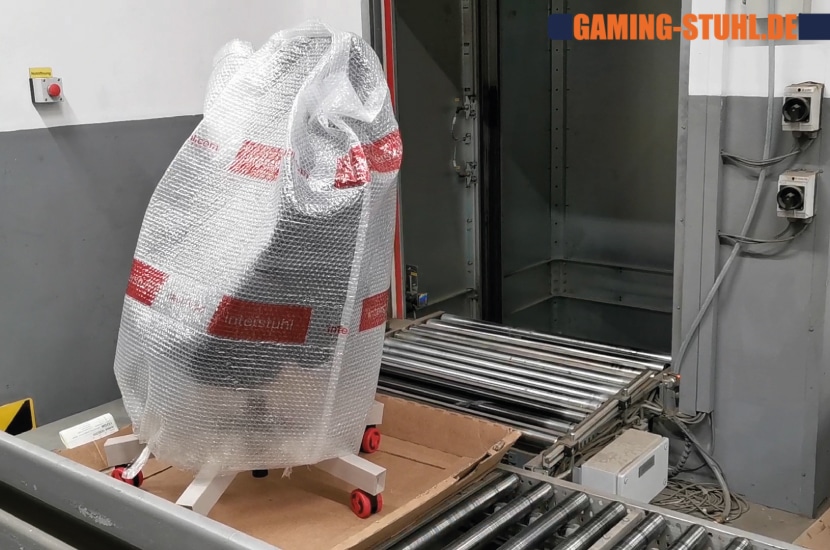
So the chair goes down the elevator here and is transferred through the catacombs to the next but one part of the building.

Here it comes up again to be transported along the ceiling to the shipping department.
The laboratory - the "in-house TÜV
And now we can take a look at why, among other things, Interstuhl can afford to confidently offer a 10-year warranty on the Backforce One.
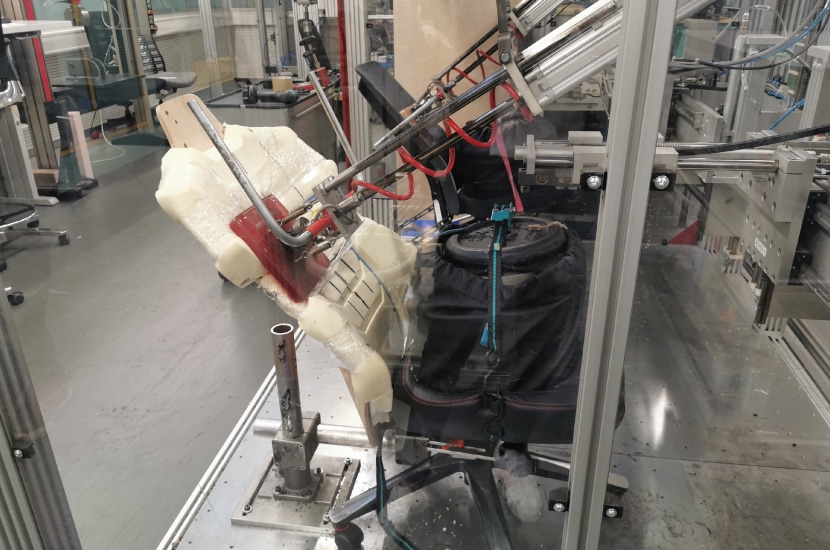
Because here you can see Interstuhl’s laboratory, where every chair can be extensively tested even before it is launched on the market.
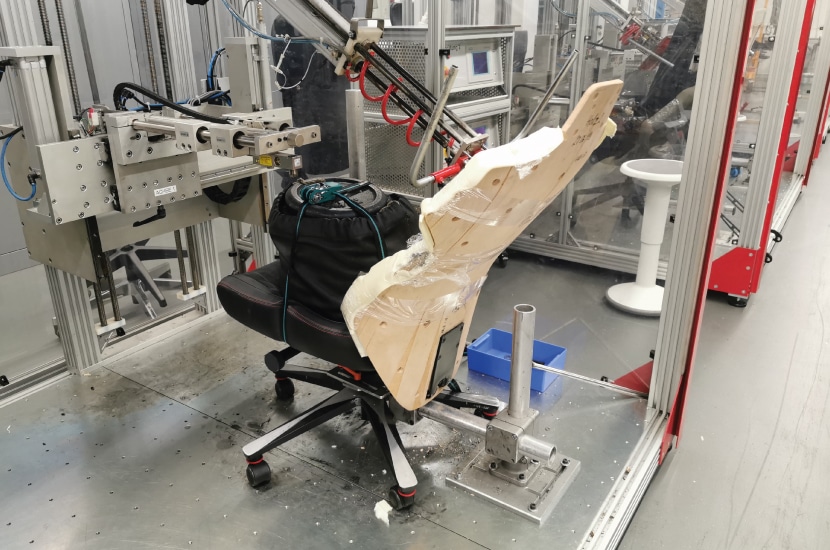
Here, every component is exposed to the daily stresses in simulated form. And you have to imagine the processes you see here over many hours. For example, the chair is leaned against several 10,000 times over a specified period of time to make absolutely sure that its design functions properly.
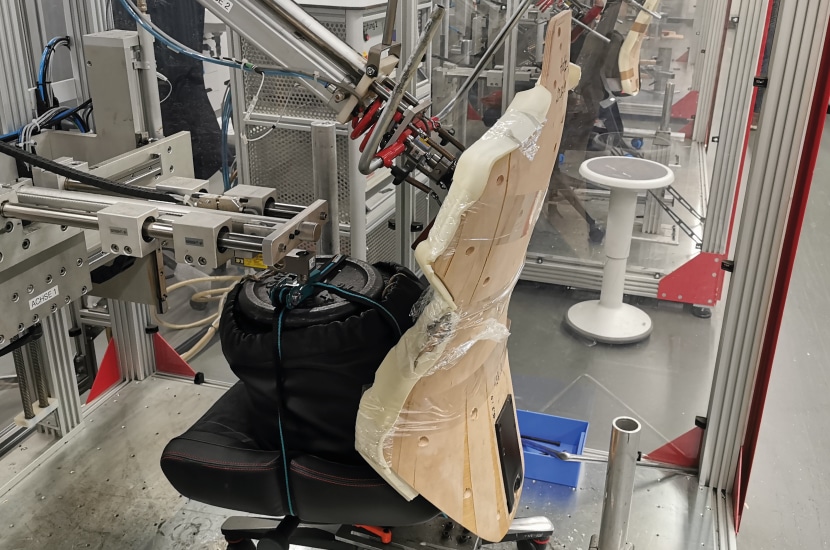
In this way, the product can be optimized to near perfection even before it is launched on the market, because many sources of error can be eliminated in advance, enabling a mature & robust product to be launched on the market.
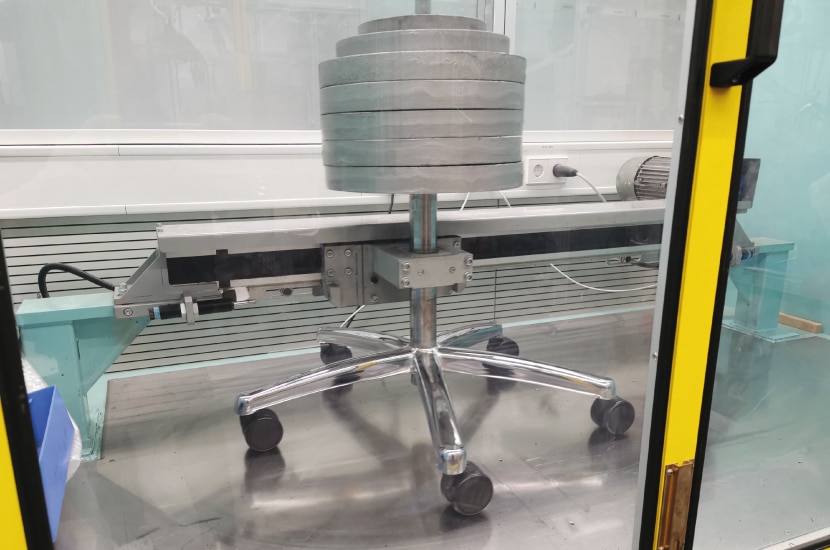
Everything is tested here: Frequent sitting down is simulated on the seating surfaces with corresponding weights, the castors are tested for their load-bearing capacity with heavy weights, backrests & mechanisms are subjected to heavy loads, and the cover fabrics are also subjected to abrasion tests.
For Interstuhl, the laboratory is virtually the company’s own TÜV.
Sustainability & employee satisfaction at Interstuhl
In many places I was fascinated by how sustainably Interstuhl works and how they are always discovering new things to work in a way that conserves resources as much as possible. I already mentioned above that the molds for the foams are wetted with a natural material like wax instead of a plastic like silicone.
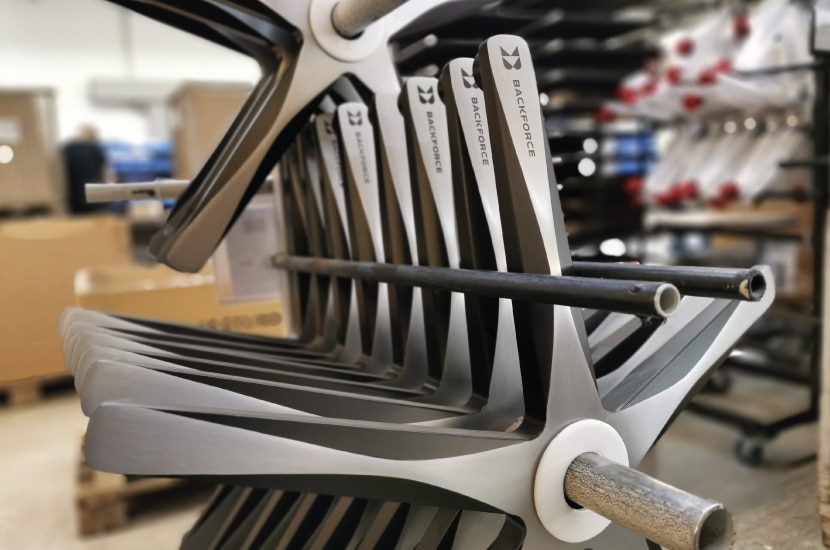
Apart from that, production is based on the just-in-time principle. The parts are hardly ever stored anymore, but produced or delivered and processed directly.
In conventional production, for example, it used to be necessary to pre-produce en masse and place them in stock. Certain pre-produced components then had to be packed, stored and unpacked again when used.

With the just-in-time principle, the produced parts are processed immediately and not stored. On the one hand, this makes production more efficient because there are fewer storage costs, and on the other hand, it is more environmentally friendly – because not every part is packaged in film and sent to the warehouse after production. There is no need to pack & store, less plastic waste is produced.
Also, the region is supported, they try to source as many components as possible from companies in the region. Even the fittings on the toilet come from a company in the region.
Water dispenser, kindergarten, homework supervision
I also noticed very positively that the company Interstuhl has its own kindergarten, including all-day and homework supervision, in order to relieve the employees. I know some big companies here from my region, but none of them offers that. That surprised me a lot.
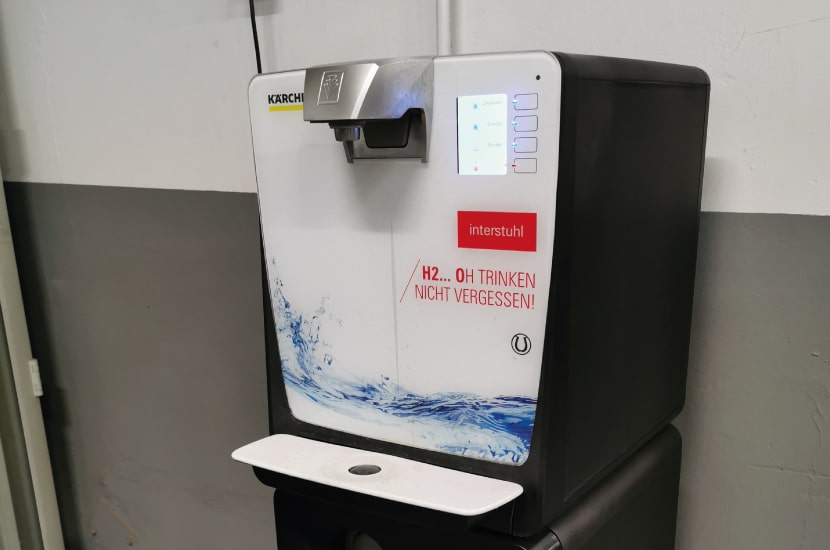
In addition, there are water dispensers all over the production site, where employees can of course fill up with water free of charge. Each employee has a bottle with his or her own name on it. They really do take good care of their employees here. And when an employee has a baby, a tree is planted on the company grounds.
Is the Backforce One really worth the money?
To construct such a chair is very expensive. The tools alone, as several manufacturers have already confirmed to me, are incredibly expensive. You have to design a tool that can be used to cast the backrest trim, for example. Such tools are incredibly expensive.
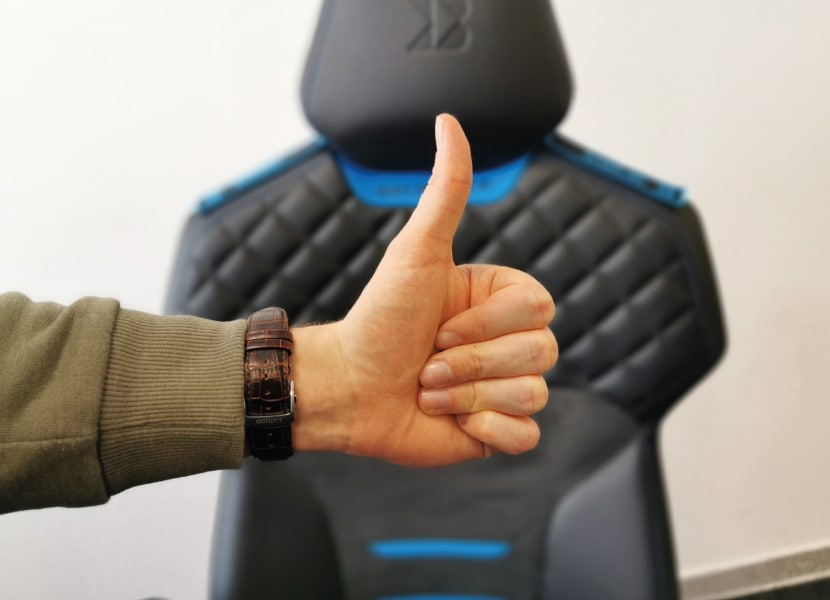
And it is precisely because such tools are so expensive that you see chairs like this so extremely rarely – upholstering and covering a steel structure is simply much more cost-effective.
And now you just have to think about it: Do I buy a chair from the Far East, which is produced at very low wage and labor costs and costs its $450 – or do I spend $150 more and get an elaborately and expensively produced chair, which is manufactured in Germany, is recyclable and secures jobs in Germany?
Even before I was allowed to visit the production, I was excited about the Backforce One. A high-quality German chair that is worth every penny. After my visit in Meßstetten-Tieringen I am even more convinced. If this high class gaming chair fits your body, I can only recommend you to buy it!
Many thanks to Stefan, Ecki, Holger & the whole Interstuhl team. The visit with you was great fun!